首页 -> 2007年第8期
液压系统泄漏的原因及对策
作者:陈林生
关键词:液压系统;泄漏;对策
液压传动技术诞生于18世纪,随即得到迅猛发展。今天,各种液压传动设备在不同行业中得到了广泛应用,在现代化机床上的应用尤为普遍。液压传动是一种以液压油作为工作介质,利用液体压力传递动力和进行控制的传动方式。它具有传送能量大、布局容易、结构紧凑、传动平稳、便于频繁换向和过载保护,并且各种元件容易实现系列化、标准化、通用化等优点,因而液压传动技术已经成为机械工业发展的一个重要推动力。但是,液压系统不可避免地会出现泄漏现象,系统的泄漏不仅严重影响了系统工作的安全性,也造成油液浪费、污染周围环境、增加机器的停工时间、降低生产率、增加生产成本以及产品污损等现象的出现。因此,对液压系统的泄漏必须加以预防和控制。液压系统产生泄漏的原因十分复杂,学生很难掌握。本文结合生产实践分析液压泄漏产生的原因,使学生对此有一个清晰的认识,从而为他们进入企业后能够解决和处理液压泄漏问题,提供宝贵的经验。
液压泄漏的种类
在分析泄漏产生的原因之前,首先要知道什么是泄漏,还要了解液压系统泄漏的种类。泄漏是指在液压系统正常工作的情况下,从液压元件的密封间隙漏出少量油液的现象。液压系统泄漏主要有外泄漏和内泄漏两种:油液从液压元件的高压腔流向低压腔的现象称为内泄漏;油液从系统内部流到系统外部的泄漏称为外泄漏。如图1所示:油液从②流向①,称为内泄漏,油液从②流向③,称为外泄漏。又如,SZ—100/80型注塑机压系统的泄漏主要有两种:固定密封处泄漏和运动密封处泄漏。固定密封处泄漏的部位主要发生在缸底、各管接头的连接处等,称为外泄现象;运动密封处泄漏主要发生在油缸活塞杆部位、多路阀阀杆等部位,称为内泄现象。

液压系统泄漏的主要原因
在企业调研中,我们分析了液压系统产生泄漏的几种原因。发现液压系统的泄漏一般都是在系统运行一段时间之后产生的,主要是由密封元件的设计加工和装配、油液受到污染、系统的冲击和振动等不良现象引起的。
密封元件引起的泄漏液压系统的可靠性在很大程度上取决于系统密封元件的设计和装配的质量。由于密封结构设计不合理,如在设计中没有考虑到液压油与密封材料的相容形式、负载情况、极限压力、工作速度大小、环境温度变化、沟槽的加工是否达到要求等;同时,又由于密封元件安装不当,引起表面磨损,造成密封配合的精度不符合要求,这些都在不同程度上直接或间接地造成了系统泄漏。另外,由于密封元件使用时间过长,出现老化、损伤、压缩量不够等现象,使得密封元件失效,也会造成泄漏。
油液受到污染引起的泄漏油液受到污染就会引起液压系统的各种故障。统计表明,液压系统的故障中,75%以上是由油液选择不当或油液污染引起的,液压油受污染后形成的微小固体颗粒会加速相对滑动零件表面的磨损,划伤密封件,从而引起泄漏,同时,颗粒污染也是加快液压元件损坏的重要因素之一。另外,液压油缸是注塑机液压系统的主要执行元件,其活塞杆导向套上装有防尘圈及密封元件,但是,由于在工作过程中,活塞杆裸露在外,直接和环境接触,所以,难免将尘埃、污物带入液压系统,加速密封元件和活塞杆等的划伤和磨损,从而引起泄漏。
系统的冲击和振动造成管接头松动引起的泄漏根据塑料注射成型工艺的需要,SZ—100/80型注塑机液压系统应满足足够的合模力、注射座可整体前进与后退、注射压力和速度可调节等要求,其工作循环如图(2)所示。注塑机通常要将熔融的塑料以40~150MP的高压注入模腔,使系统的压力发生改变、注射座的前进和后移使系统的速度产生变化,并且在此过程中产生冲击和振动,同时,管路内部流动的油液因快速的换向和阀口的突然关闭而在瞬间形成很高的压力峰值,使管接头产生松动或将密封圈挤入间隙损坏,以致造成泄漏。
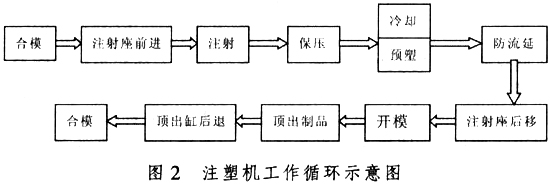
总之,在讲解液压系统泄漏时,一定要大量结合工业实际应用中常见的故障进行分析,让学生真正了解泄漏产生的原因,提高处理问题、解决问题的能力。
液压系统泄漏的防治对策
仅仅了解泄漏产生的原因是不够的,更重要的是要掌握液压系统泄漏的防治对策。导致液压系统泄漏的原因是多方面的,以现有的技术和材料,很难从根本上消除液压系统泄漏。但是,可以从液压系统泄漏的原因出发,采取合理的措施减少泄漏的发生。
(一)密封元件引起泄漏的防治对策
首先,要合理设计和加工密封件沟槽。在教学演示中,直接取出液压缸中的活塞杆,让学生观察沟槽形状,告诉他们如果液压缸密封沟槽的设计、加工达到标准、要求,就能够减少泄漏、防止油封过早损坏;否则,将会影响密封效果。密封沟槽的形状、尺寸公差、形位公差和密封面粗糙度的设计和选用,应严格按照有关标准及手册的要求执行。合理设计静密封件的密封槽尺寸及公差,可使安装后的静密封受到一定挤压,产生变形,以便填塞配合表面的微观凹陷,并把密封元件内的压力提高到高于被密封的压力,从而避免泄漏的产生。
其次,密封表面的粗糙度要适当。液压系统相对运动副的表面粗糙度由密封设计和加工情况决定。粗糙度过高或出现轴向划伤时,就会发生泄漏;粗糙度过低达到镜面时,密封圈的唇边就会刮去油膜,使油膜难以形成,密封唇口温度迅速升高,加剧磨损。所以,密封表面及其与密封圈接触的滑动面都要有适当的粗糙度。当液压缸、滑阀等的杆件出现轴向划伤时,如果划伤的程度较轻,可用金相砂纸打磨,如果划伤严重则需要进行电镀修复。
再次,要正确装配密封圈。装配前,应对零件进行仔细检查;装配时,应在零件表面涂少许液压油,轻轻压入;清洗时,应该选用柴油,特别是密封圈、防尘圈、O形圈等橡胶元件一定要用柴油清洗,如果使用汽油则易使其老化失去原有弹性,从而失去密封机能。上课时,可以拿出挂图让学生观察每种封圈的安装要求。告诉学生在装配V型、Y型、YX型等有方向性的密封圈时,应该将唇口对着压力油腔,否则密封圈就起不到应有的作用。还要告诉学生,在操作时应该注意保护唇口,以免因被零件的锐边、毛刺等锋口划伤而失去密封作用。对于旋转接触密封面(如液压泵输出轴端)而言,应选用双唇密封圈。O形圈虽然简单,但是,由于它在受到较大油压时,密封效果不理想,所以在使用时,应该加上挡圈。
(二)油液污染的控制
液压油污染的原因十分复杂,加之液压油自身也在不断产生油污,因此要彻底防止污染是很困难的。为了延长液压元件的使用寿命,保证液压系统正常工作,减少泄漏,切实可行的办法就是将液压油污染程度控制在某一限度以内。实用中常采取如下几种措施控制污染:
第一,减少外来污染。液压装置组装前后必须进行严格清洗,油箱通大气处要加装空气过滤器,并且通过过滤器向油箱灌油,维修拆卸元件时,应在无尘区进行。油箱内壁一般不要涂刷油漆,以免在油中产生沉淀物质。
第二,滤除系统产生的杂质。应在系统的有关部位设置适当精度的过滤器,并且定期检查、清洗或更换滤芯。新油加入油箱前,要经过静放沉淀,过滤后方可加入系统中,必要时可设中间油箱,进行新油的沉淀和过滤,确保油液的清洁度。
第三,控制液压油的工作温度。液压油的工作温度过高会对液压装置产生不利影响,且油温升高,会使粘性下降,增加泄漏量。液压油本身也会加速氧化变质,产生各种生成物,缩短其使用寿命。液压系统的工作温度最好控制在65℃以下,机床液压系统则应控制在55℃以下,若油温过高,则应给油箱加冷却器降温。
第四,定期检查更换液压油。应根据液压设备使用说明书的要求和维护保养规程的规定,定期检查更换液压油。比较科学的方法是定期取样化验,观察油液的变质情况,以决定是否需要换油。换油时要清洗油箱,冲洗系统管道及元件。
(三)减少系统的冲击和振动
注塑机液压系统的冲击主要产生在变压、变速、换向的过程中。此时管路内流动的液体因为快速地换向和阀口的突然关闭,而在瞬间形成很高的压力峰值,使连接件、接头与法兰松动,密封圈挤入间隙或损坏,造成泄漏。为了减轻冲击和振动,可以采取以下措施:(1)使用减振支架固定所有管子以便吸收冲击和振动;(2)延长阀门开、关和运动部件制动换向的时间;(3)适当加大管道直径,尽量缩短管路长度,管道宜采用软管,以增加系统的弹性;(4)尽量减少管接头的使用数量,管接头尽量用焊接连接。
液压系统的泄漏问题是当前机床使用过程中的重要研究课题,要让学生明白不能只是单纯地加强密封,而要系统地消除泄漏的根源,并采取有效措施予以治理。总之,讲授液压泄漏问题一定要与实际应用相联系,这样才能提高学生分析、解决实际问题的能力,提高学生工程应用的素质。
参考文献:
[1]机械基础(第三版)[M].北京:中国劳动社会保障出版社,2001.
[2]夏志新.液压系统污染控制[M].北京:机械工业出版社,1993.
[3]机床故障诊断与检修丛书编委会.机床液压系统常见故障诊断与检修[M].北京:机械工业出版社,1998.
[4]邱国庆.液压技术与应用[M].北京:人民邮电出版社,2006.
作者简介:
陈林生(1969—),广州市高级技工学校讲师,研究方向为职业教育学。(本栏责任编辑:郝茵)